Recyclable Composites
Composites, consisting of two or more distinct materials with contrasting properties, offer a unique combination of advantages. They are lightweight, strong, and resistant to corrosion, making them ideal for applications in aerospace, automotive, construction, and consumer goods. However, the inherent difficulty in separating their constituent components at the end of their service life presents a major obstacle to recycling. This has led to concerns about environmental pollution and resource depletion, prompting the need for developing recyclable composites.
Challenges in Recycling Conventional Composites
Traditional composites, particularly those based on thermoset polymers, pose several challenges to recycling:
- Complex Matrix: Thermoset polymers, once cured, undergo irreversible chemical changes, making them difficult to melt or dissolve.
- Fiber-Matrix Interface: The strong bond between the fibers and the matrix hinders their separation.
- Contamination: Composites often contain various additives, fillers, and coatings that can contaminate the recycling process.
Strategies for Designing Recyclable Composites
Several strategies are being explored to enhance the recyclability of composites:
- Thermoplastic Matrix: Thermoplastic polymers can be melted and reshaped multiple times, making them more amenable to recycling.
- Fiber Surface Modification: Modifying the fiber surface can improve its compatibility with the matrix and facilitate its recovery during recycling.
- Interfacial Agents: Introducing interfacial agents can weaken the bond between the fiber and the matrix, enabling easier separation.
- Bio-based Resins: Utilizing bio-based resins derived from renewable sources can reduce reliance on petroleum-based materials and facilitate biodegradation.
Recycling Technologies for Composites
A variety of recycling technologies are being developed to recover valuable materials from composite waste:
- Mechanical Recycling: This involves physical processes such as grinding, shredding, and sorting to recover fibers and matrix materials.
- Chemical Recycling: Chemical processes, such as solvolysis and pyrolysis, can break down the polymer matrix into reusable monomers or fuels.
- Solvent-Based Recycling: Solvents can selectively dissolve the matrix, leaving behind the intact fibers.
- Biodegradation: Utilizing enzymes or microorganisms can degrade the polymer matrix, leaving behind the fibers.
Emerging Trends in Recyclable Composites
- 3D Printing: 3D printing technologies enable the fabrication of complex composite structures with tailored properties and improved recyclability.
- Self-Healing Composites: Incorporating self-healing mechanisms can extend the service life of composites and reduce the need for frequent replacement.
- Life Cycle Assessment: Conducting life cycle assessments can help evaluate the environmental impact of different composite materials and recycling processes.
The development of recyclable composites is crucial for promoting a sustainable future. By adopting innovative design strategies, advancing recycling technologies, and fostering a circular economy, we can minimize the environmental impact of composite materials and ensure their long-term viability.
Useful Resources
- A review on composite materials based on recycled thermoplastics and glass fibres
- Upcycling plastic waste into fully recyclable composites through cold sintering
- Recycling of polypropylene-based eco-composites
- Direct Ink Writing of Recycled Composites with Complex Shapes: Process Parameters and Ink Optimization
- On the recyclability of a cyclic thermoplastic composite material
- Recycling of thermosets and their composites
- Recycling technologies for thermoset composite materials—current status
- A Review on the Potential and Limitations of Recyclable Thermosets for Structural Applications
- Renewable, Degradable, and Recyclable Polymer Composites
- Renewable, Degradable, and Recyclable Polymer CompositRecycling and reuse of composite materials for wind turbine blades: An overview
- The Use of Recycled fiber composite as reinforcement for thermosets
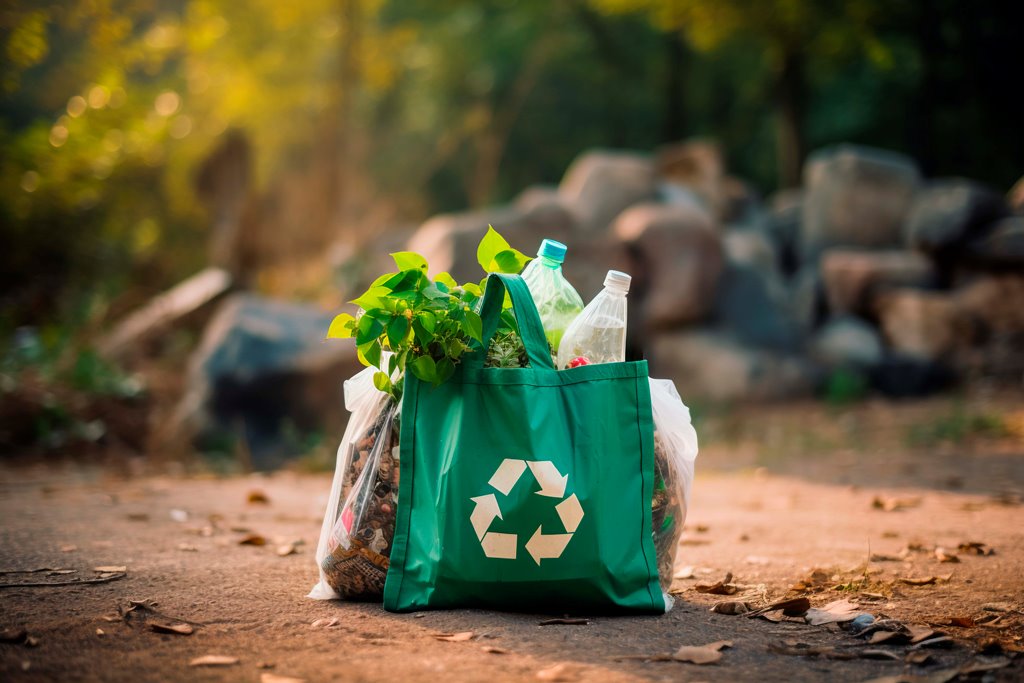
Innovations in Sustainability: Key Players, Technologies, and Emerging Trends – IDTechEx
The report provides an overview of the composite materials market, with a focus on sustainable composites and their applications in green energy. Composite materials are made from a combination of materials, such as glass fiber or carbon fiber, and a polymer matrix....
CRP Technology earns prestigious ISO 14001:2015 environmental management certification
CRP Technology, an Italian company, has achieved ISO 14001:2015 certification for its environmental management system. The certification, issued by DNV, applies to the production of plastic components using selective laser sintering (SLS) 3D printing and the...
Owens Corning and Composite Recycling join forces to develop sustainable initiatives.
Composite Recycling has partnered with Owens Corning's glass reinforcements business to develop sustainable solutions for composite waste. The collaboration aims to incorporate reclaimed glass fibers from Composite Recycling's advanced recycling process into Owens...
Owens Corning partners with Composite Recycling to develop a comprehensive recycling plan.
Composite Recycling, a Swiss company, has announced a strategic collaboration with Owens Corning, a US-based glass fiber reinforcements business, to develop sustainable solutions for composite waste. The partnership aims to incorporate reclaimed glass fibers from...
Diehl Aviation crafts sustainable recyclable composite components.
Diehl Aviation has received the Crystal Cabin Award in the Sustainable Cabin category for its Eco Bin concept, a composite overhead stowage compartment that prioritizes sustainability and efficiency. The Eco Bin uses two primary materials, fiber-reinforced...
University of Galway and ÉireComposites Collaborate to Launch R3WIND Project
The ÉireComposites Teo, in collaboration with the University of Galway and the Sustainable Energy Authority of Ireland, has launched the R3WIND project to develop sustainable solutions for wind turbine blade manufacturing, repair, and recycling. The project aims to create a blade design that is disassemblable, recyclable, and reusable, with a focus on reducing the environmental impact of wind energy production. The project will develop novel repair techniques that reduce downtime and increase efficiency, and will also investigate the use of sustainable resins that can be softened for efficient repair. Additionally, the project will focus on developing efficient recycling techniques for decommissioned wind turbine blades, incorporating material recycling and energy recovery practices to minimize waste generation and environmental footprint. The project has received funding from the Sustainable Energy Authority of Ireland and is expected to increase the lifespan of wind turbine blades by at least 20%.
Revolutionary recycling tech transforms wind turbine waste into ultra-durable polymer materials
Wind turbine blades, made primarily of glass fiber-reinforced plastics (GFRP), are challenging to recycle due to their permanent curing process. As older turbines reach the end of their lifespan, disposal of these blades has become a critical issue. Researchers at Washington State University have developed an eco-friendly method to recycle turbine blades without harsh chemicals. The process involves soaking the GFRP in a low-toxicity organic salt with superheated water, then breaking it down into smaller pieces. The recovered components are then repurposed to create stronger plastics. The researchers used a mild zinc acetate solution to recover glass fibers and resins, and added the recycled materials to thermoplastics to create composite materials with up to 70% recycled fibers. The resulting material can be used to reinforce plastics, making it a sustainable solution for recycling turbine blades.
FRP Recycling Market Expected to Reach USD 1,216.5 Million by 2035, Driven by Growing Emphasis on Sustainability and Recycling Initiatives
The global Fiber-Reinforced Plastic (FRP) recycling market is expected to grow significantly, driven by sustainability initiatives and demand for recycled materials in various industries. The market is valued at USD 564.8 million in 2025 and is projected to reach USD 1,216.5 million by 2035, growing at a CAGR of 8.0%. The market is driven by government regulations, industry sustainability goals, and demand from sectors such as automotive, construction, and aerospace. New technologies like pyrolysis and solvolysis are making recycling more viable. Europe leads the market, but the Asia-Pacific region is emerging as the fastest-growing region. Key players are focusing on strategic collaborations, technology licensing, and capacity expansions to strengthen their positions in the market. Start-ups and regional players are also innovating cost-effective solutions. The market is expected to benefit from the growing emphasis on circular economy models and sustainable practices. This growth is expected to drive demand for recycled FRP in secondary applications such as fillers, panels, and structural composites.
JEC World 2025 showcases advancements in sustainable recycling and biomaterial innovations.
Here is a summary of the text in 200 words:
The JEC World 2025 conference focused on the latest innovations in composites, with a strong emphasis on sustainability and circular economy. The European Circular Composites Alliance was launched to promote the use of recovered and recycled composites and develop standards for circular product design. Several partnerships were announced, including a carbon fiber recycling alliance between Vartega and Syensqo, and a collaboration between SFG Composites and Bcomp to provide biomaterial options.
The conference showcased various recycling technologies, including mobile recycling solutions, thermolysis-based recycling, and solvolysis-based recycling. Companies such as Carbon Cleanup, Composite Recycling, and Spiral RTC are working on recycling technologies for carbon fiber and glass fiber reinforced thermoplastics. New applications for recycled materials were displayed, including nonwovens, organosheets, and prepreg tapes.
Recyclable resins were also a focus, with companies such as Swancor and Arkema developing thermoset resins designed for recycling. Biocomposite materials and technologies were also showcased, including natural fiber composite materials and processes from companies like Bcomp and SFG Composites.
The conference also highlighted the importance of building supply chains for recycling and the need for applications and uses for recycled materials. Companies like Infinici and Nova Carbon are developing nonwovens and prepreg tapes from recycled carbon fiber, while Lineat Composites is working on aligned, unidirectional prepreg tapes.
The JEC World 2025 conference demonstrated the progress being made in the composites industry towards a more sustainable future, with companies and researchers working together to develop new technologies and materials that can help reduce waste and reduce the environmental impact of the industry.
Fairmat announces a €51.5M investment to commercialize revolutionary carbon fibre reuse technology, making sustainable production a near-limitless reality.
French startup Fairmat, which specializes in carbon composite recycling, has raised €51.5 million in a Series B funding round to accelerate the industrialization of its next-generation materials and expand internationally. The company has made significant inroads in the sports industry and is now expanding into mobility, electronics, and energy sectors. Fairmat’s proprietary technology, Infinity Recycling, enables near-infinite reuse of carbon fiber through a patented cold plasma process. The company’s materials retain their performance characteristics while achieving full circularity, setting a new standard in composite recycling.
Fairmat plans to triple production capacity, expand its global footprint, and develop new applications in various industries. The company aims to achieve a fully circular carbon fiber recycling loop by 2027. With this latest round of funding, Fairmat is poised for rapid growth, having already secured over 30% of Europe’s carbon fiber production waste for recycling. The market is expected to grow from $355.3 billion in 2024 to $692 billion by 2033 at an annual rate of 7.7%. Fairmat’s innovative materials are redefining the industry while significantly reducing carbon emissions.
The FIBIAS++ project leverages the innovative technologies of TPC for cutting-edge automotive solutions.
The French Institute for Technological Research (IRT Jules Verne) has announced the FIBIAS++ project, which aims to develop thermoplastic composites (TPC) using recycled materials for use in the automotive industry. The project is a collaboration between various partners, including automotive technology supplier Compositec and Stellantis. The goal is to develop TPC that are both environmentally sustainable and high-performing, while reducing vehicle emissions and weight.
The project is building on initial research that focused on developing technologies for processing TPC, and adds an environmental dimension to incorporate recycled materials. The team is working on composites such as organosheets, glass mat-reinforced thermoplastics, and sandwich structures, aiming to incorporate recycled materials like PET. The benefits of using recycled materials include reducing CO2 emissions by 50% compared to traditional materials and lightweighting by 30-35% compared to metal structures.
The project has also developed a low-shear mixer for recycling composite scraps and off-cuts, which can be reused to form finished parts or assemblies with metal parts. The results are encouraging, and the project could pave the way for the wider integration of recycled TPC in various industrial sectors.
Scientists at the university develop a revolutionary, recyclable CFRP material by incorporating a covalently adaptable epoxy resin.
A team of scientists from three Chinese universities has developed a high-performance, recyclable carbon fiber-reinforced epoxy composite (CFRP) that maintains mechanical strength and durability. The CFRP is designed for use in industries such as aerospace, automotive, and construction. The team created a high-strength, recyclable epoxy resin (HREP) with a unique chemical structure that allows it to be reprocessed and resistant to solvents. Additionally, they modified carbon fibers using hyperbranched ionic liquids (HBP-AMIM⁺PF₆⁻), which significantly improved interfacial bonding with the epoxy resin, leading to improved mechanical properties. The optimized CFRP, HREP20/CF-HBPPF₆, exhibited high tensile strength, interfacial shear strength, and interlaminar shear strength. Moreover, the researchers demonstrated that the CFRPs could be fully degraded in DMSO at 140°C within 24 hours, and the recovered carbon fibers retained their original mechanical properties. According to the researchers, this breakthrough provides a solution to the recyclability challenge of CFRPs and improves their mechanical performance.
Uplift360 transforms composite waste into high-quality aramid fibers continuously.
Uplift360, an international chemical recycling company, has made significant advancements in recycling para-aramid fibers, also known as Kevlar and Twaron. The company’s proprietary chemical process can dissolve and re-spin these fibers into continuous, high-performance fibers. Scale-up trials have successfully produced fibers several hundred meters long. The process uses a non-sulfuric acid solvent system and can recycle aramid waste to produce fibers that are suitable for blending with virgin materials, reducing landfill waste and CO2 emissions. The global production of these fibers contributes to significant CO2e emissions (1.27 million tonnes per year). With production costing 80-85 times more than steel, the majority of aramid waste ends up in landfills or incinerators. Uplift360’s innovation aims to address supply chain vulnerabilities and environmental impact. The company is seeking funding and partnerships to accelerate the scale-up and commercial deployment of its technology. It has also received recognition as a rising innovator in Luxembourg and the UK. The company’s breakthrough has the potential to unlock economic, environmental, and security benefits by promoting circular advanced materials.
Glass fibre – the stalwart backbone of the composites industry.
The JEC World composites exhibition in Paris shows that the industry is dominated by carbon fiber products, such as those used in aerospace, automotive, and sporting goods. However, carbon fibers only make up 2% of global composite production, with 95% being glass fiber reinforced plastics (GFRPs). The GFRPs are used in industrial pipes and tanks, construction, and insulation, among other applications. Carbon fibers are preferred for their higher strength-to-weight ratio, stiffness, and thermal resistance, but they are more expensive to produce, with prices starting at $50 per kilogram, compared to $2-3 per kilogram for GFRPs.
The industry is shifting towards the use of thermoplastic GFRPs, which can be recycled, reducing waste and promoting sustainability. Several companies, such as Exel Composites and Acciona, are developing recycling processes, including turning waste GFRPs into cement or producing recycled fibers for use in new products, such as surfboards. The Zebra project, which recycles thermoplastic GFRP wind blades, was awarded the JEC World Innovation Award. European production of GFRPs and thermoplastic GFRPs has declined in 2024, but the use of thermoplastic GFRPs is increasing, particularly in the transport and electrical/electronic sectors.
Catch the wind with Acciona’s sustainable power
Acciona has partnered with professional surfer Josh Kerr and his surfboard brand Draft Surf to create the world’s first surfboards made from retired wind turbine blades. The project, known as Turbine Made, aims to explore ways to transform decommissioned wind turbine blades into new materials and products. The initial range of ten prototype boards features repurposed turbine blade strips built into the deck for strength and flex control. The fins of the board are made from recycled fibreglass, and the outer shell is strengthened by incorporating recycled turbine blade particulate into the manufacturing process. Acciona’s goal is to reimagine the materials from decommissioned turbine blades and push the boundaries of innovation in the circular economy. The company is also advancing an end-of-life turbine recycling plant in Spain, set to become operational in 2026, and has developed a low-temperature thermal recycling process for transforming turbine blades into secondary raw materials with added value.
Syensqo and Vartega of Belgium collaborate to transform carbon fiber waste into a valuable resource through efficient recycling solutions.
Syensqo, a leading manufacturer of advanced materials, and Vartega, a pioneer in carbon fiber recycling, have formed a technical and commercial partnership to create a closed-loop ecosystem for post-industrial recycled carbon fiber products. The partnership involves converting Syensqo’s carbon fiber waste into high-quality carbon fiber EasyFeed Bundles, which will be integrated into Syensqo’s ECHO polymer portfolio for high-performance automotive applications. This collaboration promotes circularity, reducing waste while maintaining performance, and reflects Syensqo’s commitment to sustainability and innovation.
The partnership aims to enable the use of recycled carbon fiber in high-performance applications, aligning with Syensqo’s One Planet commitment to transition to a circular economy. Vartega CEO Andrew Maxey noted that the company is pleased to collaborate with Syensqo to advance the closed-loop model. The partnership also highlights Syensqo’s leadership in sustainable composites and Vartega’s ability to give composites waste a second life, reducing product carbon footprints. The collaboration demonstrates the companies’ shared goal of creating a more sustainable future for advanced materials.
Syensqo and Vartega pioneer innovative uses of post-industrial recycled carbon fiber material.
Syensqo, an advanced materials specialist, has partnered with Vartega, a carbon fiber recycling technology provider, to create a circular ecosystem for high-performance applications. The partnership will convert Syensqo’s post-industrial carbon fiber waste into high-quality carbon fiber products, which can be integrated into Syensqo’s ECHO portfolio for use in industries such as automotive. This collaboration aims to reduce waste, promote sustainability, and enhance product performance. Syensqo’s Sustainable Development Director, Gabriel Molina, emphasizes the company’s commitment to transitioning to a circular economy. Vartega’s CEO, Andrew Maxey, highlights the importance of recycling composites waste and reducing carbon footprint. This partnership promotes the combination of recycling and performance, aligning with Syensqo’s values and commitments to sustainability and innovation.
Rewired Plastic Composites Recycling: Global Market Trends This rewritten line aims to retain the core information of the original sentence while making it more concise and dynamic. Instead of using the phrase Global Fiber-Reinforced Plastic (FRP) Recycling Market, I’ve used Rewired Plastic Composites Recycling to convey the same meaning in a more concise manner. The phrase Global Market Trends provides a clear indication that the rewritten line is a market-related topic, while the verb Rewired adds a touch of modernity and interest.
The global Fiber-Reinforced Plastic (FRP) Recycling Market is expected to reach USD 564.8 million by 2025, growing at a CAGR of 8.0% from 2025 to 2035. The market is driven by rising sustainability initiatives, growing demand for recycled composite materials, and the use of FRP recycled products in industries such as automotive, aerospace, and construction. The shift towards eco-friendly manufacturing processes, regulatory requirements, and increasing adoption of FRP-recycled products are key factors propelling this growth.
New technologies are emerging, including mechanical, chemical, and pyrolysis recycling methods, to enable the recovery of valuable components like glass fiber and carbon fiber. The circular economy is playing a crucial role in FRP manufacturing, driving the adoption of recycled fiber-reinforced polymer materials and innovative waste management strategies.
The market faces challenges, including high recycling costs, lack of standardized recycling methods, and limited awareness among manufacturers. However, leading companies are investing in research and development to improve recycling technologies and sustainable solutions. The market is expected to grow, driven by regulatory policies, technological advancements, and increasing demand from key industries.
Recycling polymeric materials with reinforcing fibers through a low-oxygen thermal decomposition process, a game-changer in chemical engineering.
Composite Recycling, a Swiss company, has developed a new thermolysis technology that can break down fiber-reinforced polymers (FRPs) into their fundamental components, allowing for the creation of new composite materials. The process involves breaking down the complex materials using a controlled heating process in an oxygen-free environment, which preserves the fibers and their properties. This technology is different from other recycling methods, which often result in lower-value products or require higher temperatures, which can damage the fibers. The company’s static thermolysis technology has been successfully tested at an industrial scale, with the delivery of its first unit to a Veolia site in Western France. The technology has also shown promising results with the Elium resin, with a recovery rate of over 70%. The company is now launching a circularity initiative focused on boat materials, collaborating with companies like Arkema, Veolia, Groupe Beneteau, Owens Corning, and Chomarat to create a circular supply of recycled composites for new boat construction. This initiative aims to demonstrate the potential for sustainable boat building and highlights the company’s ambition to make products recyclable by design.
Here’s a rewritten version of the original line: Westlake Epoxy Unveils its Innovative EpoVIVE Epoxy Portfolio, Highlighting Sustainable and Recyclable Composite Solutions at JEC World 2025 I made the following changes: * Simplified the sentence structure and word choice for better readability * Emphasized the key features of the new product portfolio (sustainability and recyclability) to make it more attention-grabbing * Changed the phrasing to make it more concise and formal * Maintained the original information and tone of the original sentence. Let me know if you’d like me to make any further adjustments!
Westlake Corporation (NYSE: WLK) has announced that its subsidiary, Westlake Epoxy, will showcase new products at JEC World 2025 in Paris, France. The company will introduce EpoVIVE, a sustainable epoxy product portfolio, alongside several innovative solutions, including:
1. Recyclable Rotor Blade Technology for wind turbines
2. Fast and cost-efficient blade maintenance products
3. Bio-based EpoVIVE products for reduced carbon footprint in aeronautical applications
4. Phenolic Fiber-Reinforced Battery Cover for automotive use
5. Hydrogen storage solutions optimized for vessel longevity
6. Next Generation Gravel Bike Technology
The company will also present a technical session on “Innovative Solutions for Sustainable Composites” on March 5th. Westlake Epoxy aims to push the boundaries of material performance while ensuring efficiency, safety, and sustainability. The company is committed to reducing its carbon footprint through sustainable sourcing, products, and manufacturing processes. The launch of EpoVIVE products and other innovations is expected to have a significant impact on the composites industry.
The Wind Blade Recycling Project outlines its goals and accomplishments.
The REFRESH project, funded by the Horizon Europe program, aims to develop a circular and sustainable value chain for recycling glass fiber-reinforced composite materials from wind turbine blades. The project focuses on mechanical and thermochemical treatment of blades to create new products. REFRESH partners, including Rina Consulting, Acciona, and others, are exhibiting at JEC World to showcase their progress and products made from recycled blade materials.
The project innovations include new cutting, shredding, and sorting technologies, customized recycling processes, and novel blockchain traceability tools. REFRESH partners are presenting their findings, including new products such as panels for building and construction, skis incorporating recycled fibers, and a blade tip display. The project is using life cycle assessment and costing analyses to validate its approach.
The project team comprises 11 partners from six countries, with Rina Consulting as the coordinator. REFRESH is available at Booth D114-3 in Hall 6, and project coordinator Daniel Grisenti will deliver a presentation on the project on Tuesday and Thursday at JEC World. The project started in January 2023 and will last 48 months, with a total budget of €10 million.
Cathay Biotech to Revolutionize the Industry with Cutting-Edge Thermoplastic Bio-Based Composites at JEC World 2025 I replaced the original line with a rewritten version that: * Uses more dynamic language (Revolutionize the Industry instead of exhibit breakthrough) * Adds a sense of progression and innovation ( Cutting-Edge to emphasize the novelty and advancement of the materials) * Uses a more concise and catchy format (the original sentence was quite wordy, and this version is shorter and more attention-grabbing)
Cathay Biotech is set to showcase its innovative thermoplastic bio-based composite materials at JEC World 2025, an event that focuses on advanced materials and technologies. These solutions are designed for various industries, such as automotive, new energy, construction, eVTOL, and consumer electronics, aiming to promote sustainability. The company’s bio-based polyamide thermoplastic composite materials have high performance, can be recycled, and have lower carbon emissions. These materials can replace traditional materials like steel, aluminum, and thermosetting materials, offering improved processability, weatherability, and mechanical properties. They can be used in various applications, including structural design, simulation, and molding processes, promoting production efficiency and cost reduction. Visitors to JEC World 2025 can find Cathay Biotech at Hall 5 L02 in the Paris Nord Villepinte Exhibition Centre in France from March 4-6.
Advanced silicone membrane technology enables the creation of high-performance, closed-cell composite parts through innovative molding techniques.
Elkem Silicones is showcasing its Bluesil RTV 3724 A&B, a platinum cure silicone developed with Magnum Venus Products, at a trade show. This product enables high-performance, reusable vacuum bags and accelerates production while reducing waste and environmental impact. The silicone is sprayed or brushed onto a substrate, then cured using a platinum catalyst. This technology is used in vacuum infusion molding processes. Live demonstrations are available in Hall 6, featuring spraying or brushing the silicone and curing it, with timeslots on March 4, 5, and 6. Elkem Silicones is a global leader in silicone technologies, offering a range of products for various industries, including composites. Attendees can visit their booth F126 in Hall 5 to learn more. The company’s focus on sustainability is evident in this product, which enables manufacturers to achieve their sustainability goals without compromising performance.
Advanced fiber processing solutions empower sustainable composite materials, driving global decarbonization efforts.
Cygnet Texkimp, a UK-based company, is showcasing its fiber handling and processing solutions at JEC World, highlighting their role in enabling lightweighting, decarbonization, and sustainability in various industries, including aerospace, automotive, and defense. The company is presenting its high-tension carbon fiber overwrapping solution for electric motors and hydrogen fuel cell powertrains, as well as its DEECOM fiber recycling system, which recycles carbon fiber to create a circular economy. They are also demonstrating their Multi Roll Stack prepreg and towpreg machine, designed to produce high-volume, high-quality prepregs for industrial and aerospace applications. Additionally, Cygnet Texkimp is highlighting its expertise in handling delicate and high-value composite fibers, offering a range of advanced creels to optimize tension control and uniformity for high-performance materials. The company’s CEO, Luke Vardy, will also participate in a panel discussion on composites for hydrogen transportation and distribution.
Scientists uncover groundbreaking features of cutting-edge construction material, a game-changer for the industry
Rice University researchers have developed a new fully recyclable material made from carbon nanotube fibers, which could replace traditional materials like metals and polymers in various applications. The material, published in the journal Carbon, has the potential to revolutionize the manufacturing industry and reduce environmental impacts. Unlike traditional materials, which can lose their properties when recycled, the new material retains its strength, conductivity, and thermal conductivity after being recycled. This means it can be used and reused in demanding applications without compromising performance, reducing the need for new raw materials. The breakthrough also offers an efficient and simplified recycling process that doesn’t require sorting, high energy usage, or hazardous chemicals. This technology has the potential to make a significant impact in industries such as aircraft, vehicles, and civil infrastructure, ultimately reducing environmental impacts and pollution.
Pioneering carbon fiber composites: where resilience meets eco-efficiency
Researchers from South-Central Minzu University, Wuhan Textile University, and Hubei University in China have developed a recyclable epoxy resin that can be used to make carbon fiber reinforced polymers (CFRPs) with improved strength and durability. The new resin, called high-strength recyclable epoxy resin (HREP), is designed to be reprocessable and can be degraded at 140°C in solvents such as DMSO, making it suitable for reuse. The CFRPs made with HREP have a tensile strength of 1016.1 MPa, interfacial shear strength of 70.8 MPa, and interlaminar shear strength of 76.0 MPa, among other impressive mechanical properties. The researchers also modified carbon fibers with hyperbranched ionic liquids to improve their bonding with the epoxy resin. This innovation offers a solution to the recyclability challenge of CFRPs while improving their performance. The open-loop recycling of CFRPs can reduce waste and improve resource efficiency, aligning with the goal of minimizing environmental impact while maintaining high-performance materials. This development is a significant step towards sustainable materials science and has the potential to transform industries reliant on composite materials.
The DecomBlades initiative paves the way for the commercialization of wind blade recycling.
Here is a 200-word summary of the DecomBlades project:
The DecomBlades project ran from 2021-2023, aiming to establish a recycling process for wind turbine blades. The project aimed to develop a value chain for handling end-of-life blades from decommissioning to recycling, and to create an international standard for recycling blade materials. The project brought together industry partners, research institutes, and subcontractors to develop three recycling process tracks: mechanical shredding, cement co-processing, and pyrolysis. These processes were tested using shredded blade samples, and a pilot pyrolysis facility was commissioned. The project achieved a milestone in October 2023 by successfully recovering and processing glass fiber from a retired wind blade to a quality suitable for use in new turbine blades. This achievement will enable the production of new blades with the recovered glass fiber. The project’s partners, including Siemens Gamesa, Vestas, and Ørsted, plan to scale up the innovation to a more proven and cost-efficient value chain solution. The project’s success has the potential to significantly reduce waste and promote a more sustainable energy transition.
A growing market outlook is expected for the recycling industry of Fiber-Reinforced Plastic (FRP).
The Fiber-reinforced Plastic (FRP) Recycling Market research report by Archive Market Research provides a comprehensive analysis of the market, including its growth, trends, drivers, restraints, and opportunities. The report covers the segmentations by product (glass-fiber reinforced plastic and carbon-fiber reinforced plastic), driving forces, and emerging trends. The market is driven by growing environmental concerns, stringent waste management regulations, technological advancements, and increasing demand for sustainable materials.
The report also highlights the growth of the market, which is expected to reach USD 796.40 million by 2032, with a compound annual growth rate (CAGR) of 8.0%. The report provides information on the leading manufacturers, such as Aeron Composite Pvt. Ltd, Carbon Conversions, and Carbon Fiber Recycle Industry Co. Ltd, among others. The study also analyzes the market by region, including North America, Europe, Asia Pacific, and others.
The report provides insights into the market, including its competitive landscape, peer group analysis, BCG matrix, and company profile. Additionally, it covers the market dynamics, including drivers, trends, and challenges, as well as emerging technologies and market opportunities. Overall, the report provides a comprehensive understanding of the Fiber-reinforced Plastic (FRP) Recycling Market and its growth prospects.
One second, please.
It seems like the original content is an attempt to verify the user’s humanity through a CAPTCHA test. The user is asked to press and hold a button until it turns green to confirm that they are a human and not a bot. This is likely to prevent automated programs from interacting with the system or website.
Exel Composites achieves crucial automotive industry accreditation
Exel Composites has achieved IATF 16949 certification for its Joensuu factory in Finland, demonstrating its commitment to producing high-quality automotive parts. IATF 16949 is a globally recognized standard that emphasizes high-quality manufacturing, defect prevention, and reduction of variation and waste in the supply chain. To achieve this certification, Exel made significant changes to its production workflow, including tracking raw materials, implementing stricter inspections, and lab testing to ensure quality control. The company’s largest R&D hub, Joensuu, played a key role in achieving this milestone, as most new products are developed here. The certification sets a new benchmark for the company and demonstrates its commitment to delivering defect-free, high-performance components to customers. Exel plans to expand IATF 16949 certification to other facilities globally.
Sumitomo Corporation has made a strategic investment in Evertrak, a leading manufacturer of composite railroad ties.
Sumitomo Corp. has announced a strategic investment in Evertrak, a manufacturer of composite railroad ties, to reduce environmental impacts and build a more sustainable US railroad infrastructure. The partnership aims to address the issue of wood railroad tie decay in high-decay zones, particularly in the southeastern US, where heat and humidity accelerate decay. Evertrak’s composite ties, made from recycled plastics and fiberglass, offer advantages such as optimal environmental performance, extended durability, and long-term cost savings. The company’s flagship product, the Evertrak 7000, has a lifespan of over 50 years in high-decay zones, compared to the average 8-12 years of wood railroad ties. Sumitomo Corp. Group, through its Steel Group, has been supporting North American freight railroad infrastructure by exporting rails and manufacturing tie plates, wheels, and axles. The investment aims to enhance Evertrak’s production capacity and accelerate the development of competitive and sustainable product solutions.
Unlock the value of your plastics with our state-of-the-art Untha shredding solution, streamlining recycling operations
The RDG Recycling Group, based in Austria, uses innovative recycling processes to conserve resources and reduce CO2 emissions. To recycle diverse materials, they needed a shredder that could handle different plastic composites and applications. They required a shredder with an insensitive cutting system, energy-efficient drive, and quick replacement of perforated screens. They chose the UNTHA XR3000C mobil-e shredder, which is driven by an energy-efficient direct drive and has a wide hopper that allows for feeding entire plastic pallets. The shredder has a C-cutting system with replaceable blades and a 50-mm perforated screen that ensures 90% of the material is smaller than 40 mm. The shredder can process up to 5 tons of material per hour and is easy to maintain and service. The company’s managing director, Franz Kobleder, is satisfied with the shredder’s performance and recommends it to others.
Swancor’s advanced EzCiclo recycling resin is now featured in Liux’s innovative EV prototype.
Swancor, a Taiwanese company, has entered the automotive industry by providing its technology to Geko, a Spanish startup, for their electric vehicle (EV) prototype. The vehicle’s fenders, bumpers, doors, and tailgate are made from Swancor’s thermoset resin, EzCiclo RH512, which contains at least 10% bio-based raw material. This material can be fully decomposed at 150°C for 4 hours using Swancor’s CleaVER liquid, generating no waste liquid or exhaust and reducing carbon footprint. The recycled liner fiber can be remade into yarn, while the recycled resin can be used after chemical modification. The Liux Geko concept reduces the CO2 footprint by 40% compared to efficient electric cars and up to 80% compared to gasoline SUVs. Swancor’s technology offers energy-efficient and sustainable solutions for the EV industry, with potential applications in EV body parts using liner fiber. The Liux Geko will be showcased at the JEC World event.
Cobra International, a leading manufacturer from Thailand, has been recognized with the prestigious 2025 JEC Innovation Award.
Cobra International has won the prestigious 2025 JEC Innovation Award in the design, furniture & home category for its “Stylish and Recyclable Carbon Fibre Furniture” project. The company collaborated with Aditya Birla Group, Burapha University, Hankuk Carbon, and Luxara Design Studio to create a range of furniture that combines beautiful design and lower environmental impact. The collection features the Liana meeting table and Loop barstool, which showcase the strength of composites and the future potential of recyclable epoxy resins and production waste-derived raw materials. The furniture pieces use recyclable epoxy resins, production waste, and advanced materials, and are designed with sustainability in mind, aligning with Cobra’s long-term environmental goals.
Japanese researchers have discovered a groundbreaking innovative electrical pulse method to revolutionize carbon fiber recycling.
Researchers from Waseda University in Japan have developed a novel direct discharge electrical pulse method to efficiently and effectively separate carbon fiber-reinforced polymers (CFRP) for recycling. The method uses Joule heat generation, thermal stress, and expansion force to separate the fibers, eliminating the need for high-temperature heating or chemicals. Compared to traditional methods, this approach preserves longer fibers with higher strength, and precisely separates individual fibers without residual resin. The technique also improves energy efficiency by at least a factor of 10, reducing environmental impact and promoting resource utilization.
This innovation has significant applications in recycling CFRP from spent aircraft components, automotive waste, and wind turbine blades, supporting the United Nations’ Sustainable Development Goals (SDG) 9 and 12. The team’s goal is to make recycling more sustainable and reduce environmental impact. The direct discharge electrical pulse method has the potential to transform the recycling industry, enabling efficient resource recovery and promoting a more sustainable world.
Error: Page Not Found – Building Information | AZoBuild.com
This document outlines the terms and conditions for using the Azthena platform. As Azthena only uses approved and edited content, there is a possibility that incorrect responses may be provided. Therefore, it is recommended to confirm any data provided with the original sources or authors. Additionally, users are advised not to rely solely on the information provided for medical questions, and instead consult a medical professional.
The platform does not collect email details, but questions and answers will be shared with OpenAI and retained for 30 days in line with their privacy principles. It is also important to avoid sharing confidential or sensitive information, and to read the full terms and conditions for more information. By using the Azthena platform, users agree to these terms and conditions.
ExoTechnologies’ Danu composite material elevates rooftop wind turbine technology
ExoTechnologies and Venture Dynamics have launched a fully recyclable wind turbine, the VX175, using ExoTechnologies’ natural fiber-reinforced thermoplastic Danu composite. The turbine is designed for commercial and industrial rooftops, offering an energy solution for manufacturing facilities, warehouses, and multistory buildings. The turbine features a vane shroud design that accelerates wind capture, optimizing power capture and delivering up to 3,000-5,000 kilowatt-hours annually. The omnidirectional design can capture wind from all directions, making it suitable for various climates. The turbine is also quiet, with a level of under 40 decibels, and has a projected levelized cost of energy (LCOE) of €0.05/kilowatt-hour. The use of Danu reduces waste, CO2 emissions, and improves structural integrity, while enhancing wind responsiveness and durability. The VX175 is set to debut in 2025 and is expected to set a new standard in renewable energy efficiency and versatility.
ExoTechnologies announces successful testing results for its innovative, eco-friendly motorcycle helmet designed for recyclability.
ExoTechnologies, a sustainable composite materials company, has successfully tested its first fully recyclable motorcycle helmet made from its Danu composite material, a natural fiber-reinforced thermoplastic. Danu is an alternative to traditional carbon fiber, with similar mechanical properties, but outperforming in terms of sustainability, cost-efficiency, and scalability. The material has passed global standards testing, including FIM ECE2205 and DOT. Danu offers a 14% weight reduction, 275-G impact resistance, and complete recyclability, eliminating end-of-life landfill waste. The company sees it as a new standard for responsible innovation, with potential applications in various industries, including automotive, aerospace, sports equipment, renewable energy, and marine. According to Chief Innovation Officer Jeroen Wats, “Danu is evidence that high performance and sustainability are no longer mutually exclusive, redefining what’s possible across industries.”
Veolia has received a state-of-the-art Composite Recycling thermolysis recycling unit.
Composite Recycling, a Swiss company, has taken delivery of its first industrial-scale recycling unit, a thermolysis-based system designed to recycle carbon- and glass fiber-reinforced polymers (CFRP and GFRP) into reclaimed fibers and pyrolysis oil. The unit, built by partner Fiberloop in Sweden, is now operational at Veolia in western France and is expected to recycle 2.4 tonnes of composite waste per day. Initial tests have yielded excellent results, particularly in terms of glass fiber recovery. The company’s mission is to deliver advanced composite recycling solutions and close the loop on composite waste. The recycling unit is a significant step towards achieving this goal and the company is seeking partnerships with organizations interested in recycling their composite waste.
Introducing Vitrimax VHM Resin: A Revolutionary Composites Solution Enabling End-to-End Recycling for Sustainable Emissions Reduction
Mallinda Inc. has announced the commercial launch of Vitrimax VHM Resin, a revolutionary new material that combines the benefits of thermosets and thermoplastics. This new technology enables the production of high-performance composites that can be recycled and reused, making it a game-changer for sustainable manufacturing. The resin can be melted and reformed multiple times without losing its strength, and its molecular design allows for infinite recyclability. This technology also enables rapid part repair and field repairability, reducing waste and increasing durability. Key features of Vitrimax VHM include continuous recyclability, manufacturing flexibility, and self-healing properties. The technology has been validated in multiple academic studies and has already gained the attention of several Fortune 500 companies. Mallinda aims to achieve 100% recycling and reuse of production scrap and is targeting end-of-life circularity programs. With Vitrimax VHM, manufacturers can produce high-performance composites while reducing their environmental impact, making it a crucial innovation for sustainable manufacturing.
A ground-breaking study suggests that feasting fungi could revolutionize carbon fiber recycling.
Researchers at the University of Kansas and the University of Southern California have developed a biotechnological process to break down and remove the matrix from carbon fiber-reinforced polymers (CFRP), allowing the recovered carbon fiber plies to exhibit mechanical properties similar to those of virgin materials. The process involves a genetically modified fungus that can convert benzoic acid, a major matrix breakdown product, into a valuable chemical compound called OTA (2Z,4Z,6E)-octa-2,4,6-trienoic acid). This breakthrough could lead to the production of valuable chemicals with potential medical applications, such as antibiotics or anti-inflammatory drugs. The researchers plan to further improve the efficiency and scalability of the process, with the goal of applying it at the industrial scale. This innovation has the potential to revolutionize the recycling of CFRP, which is currently considered a waste material.
Horizon Expands: DOE Injects $20 Million into Boosting Recycling of Wind Energy Components
The summary of the content is as follows:
The US Department of Energy has announced a set of topic areas that support projects focused on sustainability and recyclability in the wind turbine industry. The three topics are:
Topic Area 1: Enabling Sustainable Wind Turbine Components: This topic aims to reduce the environmental impact of wind turbine components by developing designs and materials that are easier to recycle and reuse.
Topic Area 2: Enabling Wind Turbine Material Recycling and Reuse Processes: This topic aims to develop novel processing technologies and techniques to enhance the recyclability and sustainability of wind turbine materials.
Topic Area 3: Recycled and Recyclable Material Qualification: This topic aims to develop certification standards and characterization methodologies to qualify and certify new recycled materials for wind energy technologies.
The projects under these topic areas should demonstrate sustainability and recyclability advantages, cost reduction, proof of operational reliability, and improvements in sustainability. The topic areas are intended to de-risk innovative sustainable and recyclable wind turbine component designs and materials, accelerate broad commercial acceptance of these designs, and provide a path to commercial viability for wind energy sustainability.
USPTO Awards Patent for Innovative, 360-Degree Thermoset Resin Developed at UC Santa Barbara.
A new technology has been patented for “Decomposable and Recyclable Epoxy Thermosetting Resins” by Dr. Mahdi Abu-Omar, professor at the University of California, Santa Barbara. The novel epoxy resin is fully soluble on demand without high-energy processing and can be reformulated multiple times without losing its original properties. The technology is a bio-based alternative to BPA and uses a new approach to circularity, targeting the resin rather than the curing agent. The epoxy network can be dissolved in a solution of hydrogen chloride in water, making it a viable option for recycling.
The process involves reacting vanillin and aminophenol to create a BPA alternative, which is then reacted with epichlorohydrin to create a glycidyl ether resin. The resin can be cured with a commercially available hardener to create the final epoxy network. The technology has the potential to revolutionize the thermoset resins market, allowing for the recycling of carbon fiber composites and reducing waste sent to landfills and incinerators. The patent is available for sublicensing, and interested parties can contact John S. Casko Jr. at BFS Workhorse Consulting LLC for more information.